Control System Projects for Academic Excellence!
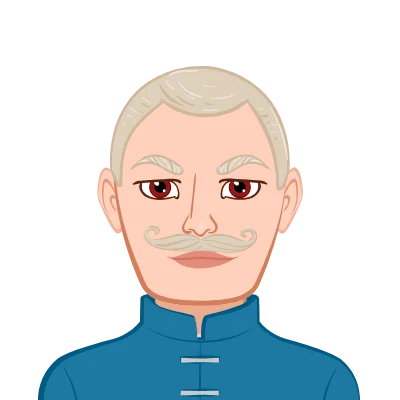
Welcome to our educational expedition into the dynamic realm of control system projects—an exciting avenue that not only unlocks the intricacies of engineering but also serves as a beacon for academic excellence. In the ever-evolving landscape of education, the integration of practical applications alongside theoretical knowledge has become imperative. This blog is your compass as we delve into the fascinating world of control systems, where theory meets real-world implementation, providing a hands-on approach to academic achievement.
As aspiring engineers and scholars, the journey toward academic excellence is often paved with challenges that demand innovation, problem-solving, and a deep understanding of core concepts. Control systems, with their pivotal role in regulating and managing dynamic systems, offer a fertile ground for cultivating these essential skills. Through this blog, we embark on a voyage that not only explores the theoretical foundations of control systems but places a strong emphasis on translating this knowledge into tangible projects.
In the dynamic realm of engineering, the study and application of control systems stand as a cornerstone for technological innovation and progress. As aspiring engineers and academics delve into the intricate world of control systems, the significance of hands-on experience cannot be overstated. This blog, aptly titled "Control System Projects for Academic Excellence," aims to be a guiding beacon for students and enthusiasts eager to elevate their understanding of control systems through practical, real-world projects. Whether you're seeking to solve your Control System assignment or aiming to deepen your comprehension through hands-on applications, this blog provides valuable insights and project ideas for academic excellence.
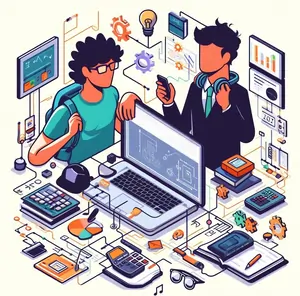
Control systems are vital in engineering, regulating dynamic systems. To enhance understanding, hands-on projects are invaluable. "Control System Projects for Academic Excellence" explores projects that not only contribute to academic success but also offer insights into real-world applications.
The field of control systems is a complex interplay of theory and application, requiring a nuanced understanding of mathematical concepts, electrical engineering principles, and computer science. As students venture into this discipline, they often find that bridging the gap between theoretical knowledge and practical implementation can be a daunting task. This blog seeks to unravel this complexity by providing a curated collection of projects that not only enhance academic learning but also foster a deeper, more intuitive grasp of control systems.
Before embarking on this educational journey, let's take a moment to understand the roadmap laid out in this blog. The projects presented here are designed to cater to a range of proficiency levels, from beginners taking their first steps into the realm of control systems to advanced learners seeking to refine their skills. Each project is accompanied by comprehensive documentation, step-by-step guides, and insightful explanations to ensure that learners not only replicate the project but also comprehend the underlying principles.
Control systems lie at the heart of countless technological marvels that shape our modern world. From automated manufacturing processes to self-driving cars, and from aerospace applications to everyday household appliances, control systems play a pivotal role in ensuring efficiency, accuracy, and reliability. Mastery of control systems is not just a feather in the cap of an engineer; it is a key to unlocking innovation and driving technological progress.
While theoretical knowledge forms the foundation of any academic pursuit, the true mastery of control systems comes from hands-on experience. Through practical projects, students can bridge the gap between theory and application, gaining invaluable insights into the challenges and intricacies of implementing control systems in the real world. This blog recognizes the transformative power of experiential learning and endeavours to provide a platform for students to engage with and apply their theoretical knowledge.
Temperature Control System
Designing a temperature control system introduces feedback control. This project regulates a system's temperature using sensors, a controller, and an actuator. Components include a temperature sensor, microcontroller (Arduino, Raspberry Pi), and a heater or cooler. Connect the sensor to the microcontroller, program it to read and compare temperatures, and activate the actuator based on deviations.
The development and implementation of a Temperature Control System represent a multifaceted exploration into the realm of control systems, a discipline crucial for managing and regulating dynamic processes. At its core, a control system is a network of devices and components working in unison to maintain a desired output or condition, often by adjusting the input. In the case of a temperature control system, the objective is to achieve and sustain a specific temperature range within a given environment.
The foundation of such a system lies in the incorporation of feedback control, a fundamental concept in control engineering. Feedback control involves continuously monitoring the system's output and adjusting the input based on the variance from the desired setpoint. This closed-loop approach ensures that the system dynamically responds to changes, maintaining stability and precision.
Central to the temperature control system are the key components: a temperature sensor, a microcontroller (such as Arduino or Raspberry Pi), and an actuator (heater or cooler). The temperature sensor serves as the system's sensory apparatus, detecting and translating temperature variations into electrical signals. These signals are then fed into the microcontroller, the brain of the system, where complex algorithms and programmed instructions determine the appropriate response.
Microcontroller programming is a pivotal skill in this context. The ability to code the microcontroller to read, analyse, and compare temperature data allows for intelligent decision-making within the system. Programming extends beyond mere temperature readings; it involves creating algorithms that govern the activation and deactivation of the actuator based on the feedback received. This step is crucial for achieving a seamless and efficient temperature regulation process.
The actuator, whether a heater or cooler, is the executive component responsible for effecting change in the system. When prompted by the microcontroller, the actuator adjusts the environmental conditions, influencing the temperature to align with the predefined setpoint. This collaborative effort among the sensor, microcontroller, and actuator encapsulates the essence of a closed-loop control system, where continuous feedback refines and optimizes the system's performance.
A critical aspect of this project is the meticulous connection of the temperature sensor to the microcontroller. Proper wiring and interfacing are essential to ensure accurate and reliable data transmission. Additionally, participants delve into the intricacies of sensor calibration, a process that fine-tunes the sensor's output to enhance accuracy and responsiveness.
Speed Control of DC Motor
Venturing into the realm of closed-loop speed control systems, this comprehensive project delves into the intricacies of managing the velocity of a DC motor with unprecedented precision and efficiency. At its core, the system integrates a powerful DC motor, a sophisticated motor driver, a high-precision speed encoder, and the central nervous system, a programmable microcontroller. This project focuses on closed-loop speed control for a DC motor. Components include a DC motor, motor driver, speed encoder, and microcontroller. Connect the encoder to the motor shaft, program the microcontroller to adjust motor voltage based on speed feedback, and experiment with control algorithms.
The focal point of this technological symphony lies in the seamless connection of the speed encoder to the motor shaft. This intricate link enables real-time feedback on the motor's rotational speed, establishing a closed-loop system wherein the microcontroller takes on the role of an orchestrator, conducting a finely-tuned control algorithm that harmonizes with the mechanical dynamics of the DC motor.
The microcontroller, endowed with intelligent programming, assumes the responsibility of dynamically adjusting the motor voltage based on instantaneous feedback from the speed encoder. This closed-loop mechanism empowers the system to adapt to varying loads and external factors, ensuring a consistent and desired speed output even in the face of changing operational conditions.
As the project's neural centre, the microcontroller is not a mere passive observer but a dynamic decision-maker. Its sophisticated programming allows it to deploy a variety of control algorithms, transforming it into a maestro conducting a symphony of electronic impulses. These impulses seamlessly blend with the mechanical nuances of the DC motor, achieving a delicate equilibrium between the desired speed and the actual performance of the motor.
Within the realm of control systems, this project serves as a fertile ground for experimentation with diverse control algorithms. The microcontroller, acting as the maestro, facilitates exploration ranging from classic proportional-integral-derivative (PID) controllers to more advanced adaptive algorithms. This experimentation not only enhances the understanding of control systems but also opens doors to optimizing the motor's response across a spectrum of operational scenarios.
In this holistic exploration, the project transcends the boundaries of a typical engineering endeavour; it becomes a journey into the marriage of mechanical precision and computational finesse. It stands as a testament to the synergistic relationship between physical components and intelligent algorithms, illustrating the power of closed-loop control systems in achieving unparalleled accuracy and reliability within the dynamic realm of DC motor speed control.
Water Level Control System
A Water Level Control System is a vital component of various industrial and domestic applications where maintaining a consistent water level in a tank is paramount. This practical project involves the integration of essential components such as a water level sensor, an actuator (in the form of a pump or valve), and a microcontroller for automated control. The primary objective is to achieve a seamless regulation of water levels, ensuring efficiency, reliability, and resource optimization. This project not only addresses practical engineering challenges but also delves into the intricacies of control systems, making it a valuable academic pursuit.
The core of this system lies in its ability to sense and respond to the water level within the tank. A water level sensor is strategically installed within the tank, equipped with the capability to measure the water level accurately. These sensors are available in various types, such as float sensors, pressure sensors, and ultrasonic sensors, each with its unique set of advantages and limitations. The choice of sensor depends on factors like the type of liquid, tank size, and the desired precision of the water level control system.
Once the sensor provides readings, the microcontroller comes into play as the brain of the system. It interprets the data from the sensor and executes control algorithms to determine the appropriate action for maintaining the desired water level. The microcontroller is programmed to activate the actuator, either a pump or a valve, based on the received sensor readings. This automated process eliminates the need for manual intervention, enhancing efficiency and precision in water level management.
In the realm of control systems, the design and implementation of control algorithms play a pivotal role. The microcontroller's programming involves the creation and optimization of these algorithms, ensuring that the water level is regulated smoothly without abrupt fluctuations. Proportional-Integral-Derivative (PID) control is a common approach employed in such systems. PID control uses a combination of proportional, integral, and derivative terms to minimize the error between the desired and actual water levels, providing a well-balanced and stable control mechanism.
In the academic context, understanding and implementing control algorithms contribute to a broader comprehension of control theory. Students engaging in this project gain practical insights into the application of theoretical concepts, bridging the gap between classroom knowledge and real-world applications. Furthermore, the project fosters a multidisciplinary approach, combining elements of electrical engineering, mechanical engineering, and computer science to create a comprehensive solution.
Quadcopter Stabilization
Quadcopter stabilization projects offer aerospace enthusiasts a captivating journey into the realms of control systems and robotics. These ventures are not merely recreational; they serve as invaluable learning experiences, providing hands-on insights into the intricate world of unmanned aerial vehicles (UAVs). At the heart of such projects lies the fusion of hardware and software, where a delicate balance is struck to ensure stability and precise control.
The fundamental components of a quadcopter stabilization project are diverse, ranging from the structural elements to sophisticated electronic components. The quadcopter frame serves as the skeletal foundation, providing structural integrity and a platform for mounting various components. The choice of materials for the frame, such as carbon Fiber or aluminium, directly impacts the quadcopter's overall weight, manoeuvrability, and durability.
Powering the quadcopter are brushless DC motors, which offer a crucial combination of efficiency and reliability. These motors provide the necessary thrust for lift and manoeuvrability, and their speed and rotation direction can be precisely controlled, contributing to the quadcopter's stability and responsiveness. Selecting the appropriate motors involves considerations such as power ratings, Kv values, and propeller compatibility.
For a quadcopter to navigate through space with stability and precision, it relies on a suite of sensors, with gyroscope and accelerometer sensors playing pivotal roles. The gyroscope measures angular velocity, helping the flight controller understand the quadcopter's orientation in three-dimensional space. Meanwhile, accelerometers gauge linear acceleration, aiding in the determination of the quadcopter's position and movement. These sensors work in tandem, supplying real-time data to the flight controller, allowing it to make rapid adjustments to maintain stability.
The brain of the quadcopter stabilization system is the flight controller, a sophisticated electronic device that processes sensor data and issues commands to the motors. Popular choices for flight controllers include Arduino and Pixhawk, both of which offer open-source platforms that facilitate programming and customization. The flight controller's firmware can be tailored to accommodate various control algorithms, enabling enthusiasts to experiment with different stabilization techniques and control modes.
Mounting the sensors onto the quadcopter frame requires precision and attention to detail. Proper sensor placement is critical for accurate data acquisition, ensuring that the flight controller receives reliable information about the quadcopter's orientation and motion. Additionally, considerations such as vibration isolation may be incorporated to minimize sensor noise and enhance overall system performance.
Programming the flight controller represents a significant phase in the quadcopter stabilization project. This involves coding the control algorithms that dictate how the quadcopter responds to external inputs and environmental conditions. Proportional-Integral-Derivative (PID) controllers are commonly employed, offering a well-established framework for achieving stability by adjusting motor speeds based on the difference between desired and actual sensor readings.
Inverted Pendulum
The inverted pendulum project challenges students to stabilize an inherently unstable system. Components include a motorized pendulum, encoder for angle feedback, and a microcontroller. Mount the pendulum, connect the encoder for angle feedback, and design a control system to keep the pendulum upright.
In the realm of control systems, the pivotal objective revolves around the creation of a robust and responsive mechanism capable of maintaining the pendulum in a perpetually upright position. The microcontroller assumes a pivotal role in this endeavour, serving as the brain that processes data from the encoder and formulates corrective actions to counteract deviations from the desired equilibrium. As students delve into the intricacies of control theory, they grapple with the dynamic interplay of concepts such as feedback loops, stability criteria, and control algorithms.
The heart of the control system lies in the ingenious utilization of feedback mechanisms. The encoder, acting as the vigilant eyes of the system, continuously monitors the pendulum's angle and relays this information back to the microcontroller. This constant stream of data forms the basis for informed decision-making, allowing the control system to dynamically adjust the motorized pendulum's position in real-time. Implementing a proportional-integral-derivative (PID) control algorithm often proves instrumental in achieving the delicate balance required for the inverted pendulum to defy its inherent instability.
Moreover, students are challenged to explore the intricacies of tuning the control system parameters to optimize performance. Fine-tuning the gains in the PID controller becomes a delicate dance, as too aggressive adjustments can lead to oscillations, while overly conservative settings may result in sluggish responses. This iterative process of experimentation and refinement not only deepens students' understanding of control systems but also hones their problem-solving skills as they navigate the complex trade-offs inherent in achieving stability in an inherently precarious system.
Beyond the theoretical aspects, the project fosters hands-on skills in hardware integration and system interfacing. Students grapple with the physical implementation of the control system, making critical decisions regarding the selection and placement of sensors, actuators, and the microcontroller itself. Wiring and connectivity challenges add an additional layer of complexity, requiring a holistic understanding of both the software and hardware aspects of control systems engineering.
The inverted pendulum project transcends the confines of a traditional academic exercise, offering a practical glimpse into the real-world applications of control systems. The ability to stabilize an inherently unstable system has far-reaching implications, extending to fields such as robotics, aerospace, and even autonomous vehicles. As students navigate the complexities of this project, they are not merely solving a theoretical problem; they are acquiring skills that are directly transferable to cutting-edge technological domains.
Conclusion
Exploring control system projects can be a transformative journey for academic excellence. We've delved into the world of practical applications, from simple circuits to complex automation systems, all of which contribute to a deeper understanding of control systems. Engaging in such projects not only enhances theoretical knowledge but also hones practical skills crucial for success in the field.
Through hands-on experiences, you've likely encountered challenges and triumphs, fostering a resilient and problem-solving mindset. The significance of bridging the gap between theory and application cannot be overstated, and control system projects provide the perfect platform for this integration.
As you reflect on the projects discussed, remember that the learning process is dynamic and ongoing. Embrace the curiosity that drove you to embark on these endeavors and carry that enthusiasm forward. Whether you're a student seeking academic excellence or an enthusiast eager to apply control system principles in real-world scenarios, the projects explored in this blog serve as stepping stones to a brighter and more informed future.
As you continue your academic journey, consider sharing your experiences with others, fostering a community of learners passionate about control systems. By doing so, you contribute not only to your own academic growth but also to the collective knowledge of aspiring engineers and enthusiasts alike.
In the realm of control systems, the journey is as valuable as the destination. May your endeavors be met with continued curiosity, perseverance, and a commitment to academic excellence. Happy engineering!