Reliability-Centered Maintenance for Control Systems: A MATLAB Toolkit

Reliability-Centered Maintenance (RCM) stands as a pivotal factor in guaranteeing the peak performance and durability of control systems within diverse industries. In the expansive realm of engineering and automation, MATLAB takes center stage as an indispensable toolkit, not only streamlining the execution of RCM strategies but also elevating the overall efficiency and reliability of control systems. This blog endeavors to delve into the profound significance of RCM for control systems while concurrently shedding light on how MATLAB emerges as an invaluable asset in this domain. At its core, RCM is a systematic approach that revolutionizes maintenance planning and decision-making, strategically allocating resources to the most critical components of a system. This proactive methodology contrasts sharply with conventional maintenance practices, ushering in a paradigm shift from fixed schedules to a targeted, consequence-driven maintenance approach. As industries increasingly recognize the paramount importance of control systems in their operations, the synergy between RCM and MATLAB becomes a linchpin for optimizing system functionality. Understanding the principles of RCM and MATLAB's role in enhancing control system reliability will be instrumental in addressing complex engineering challenges and ensuring the longevity of critical infrastructure.
Within the intricacies of control systems, where precision is paramount and downtime is a critical consideration, RCM becomes a linchpin in ensuring uninterrupted performance. It is in this context that the role of MATLAB becomes particularly pronounced. MATLAB, with its extensive suite of tools catering to modeling, simulation, and analysis, emerges as a robust platform for the implementation of RCM strategies in control systems. Beyond its role as a programming language, MATLAB serves as a comprehensive environment for engineers and practitioners, offering multifaceted solutions to address the unique challenges posed by control systems in various industries. The amalgamation of RCM and MATLAB introduces a proactive stance to maintenance in control systems, mitigating risks and optimizing reliability. This combination not only minimizes the probability of unforeseen breakdowns but also actively contributes to enhancing system availability.
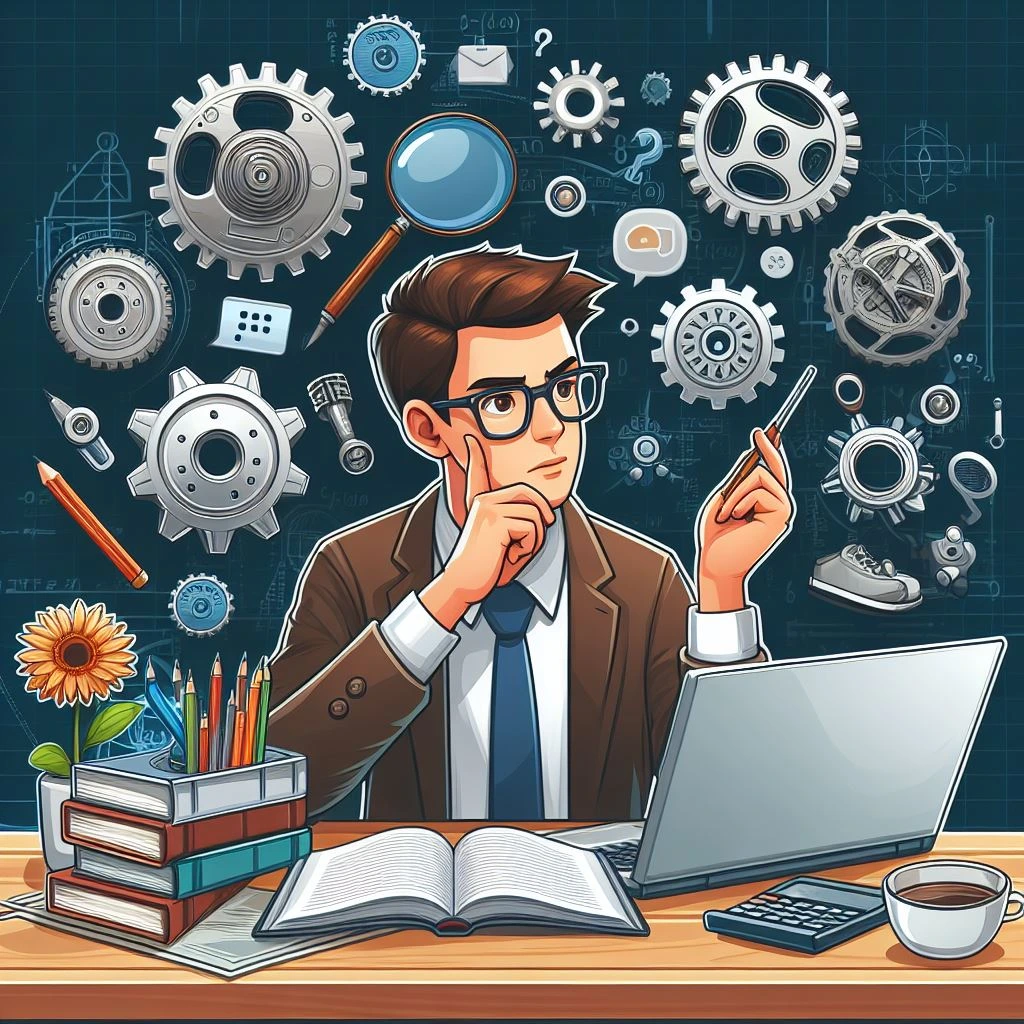
As students and professionals navigate the intricate landscape of control systems, MATLAB becomes an invaluable ally. The toolkit provides not only a conducive environment for RCM implementation but also offers a robust platform for academic and practical exploration. This is especially relevant for those seeking help with Control System assignment, as MATLAB's capabilities extend to facilitating a deeper understanding of theoretical concepts through practical application. With MATLAB, students can simulate control system scenarios, analyze reliability data, and optimize maintenance schedules – skills that are not only beneficial for academic success but also for future careers in engineering and automation.
For those seeking assistance with Control System assignments, the integration of RCM and MATLAB offers a unique opportunity for hands-on learning and practical skill development. The toolkit's versatility allows students to bridge the gap between theoretical concepts and real-world applications, fostering a holistic understanding of control systems and their maintenance strategies. As the demand for skilled professionals in control systems continues to rise, proficiency in MATLAB becomes a valuable asset, aligning seamlessly with the mission of matlabassignmentexperts.com to provide specialized assistance to students navigating the complexities of MATLAB and control systems.
In essence, the synergy between Reliability-Centered Maintenance and MATLAB not only ensures the resilience and efficiency of control systems in various industries but also provides a fertile ground for academic growth and professional development, particularly for those seeking expert assistance with Control System assignments. The journey into the intersection of RCM and MATLAB promises not only enhanced reliability in control systems but also a dynamic and engaging learning experience for students and professionals alike.
Understanding Reliability-Centered Maintenance (RCM):
Reliability-Centered Maintenance (RCM) stands as a methodical and strategic framework for maintenance planning and decision-making within complex systems. In stark contrast to conventional maintenance practices characterized by rigid schedules or reactionary responses to breakdowns, RCM embodies a proactive approach. At its core, RCM deviates from the one-size-fits-all mentality, instead directing attention and resources towards the components within a system that hold the utmost significance. This prioritization is not arbitrary; rather, it stems from a meticulous analysis aimed at identifying the critical failure modes that could compromise the system's functionality. RCM's foundation lies in understanding the potential consequences of these failure modes, both in terms of safety and operational implications. By dissecting these failure modes and their ramifications, RCM empowers decision-makers to devise maintenance strategies tailored to address specific risks and vulnerabilities. These strategies are not merely reactive measures aimed at patching up system weaknesses but rather proactive interventions designed to prevent failures before they occur. RCM, therefore, fosters a culture of foresight and pre-emptive action, wherein maintenance activities are strategically planned and executed to optimize system reliability. This approach acknowledges the inherent variability in system behavior and operating conditions, recognizing that not all components warrant equal attention or investment in maintenance efforts. Instead, RCM advocates for a targeted allocation of resources towards the critical components that have the most significant impact on system performance and safety. By focusing resources where they are most needed, RCM ensures a more efficient use of time, labor, and financial resources, ultimately leading to enhanced system reliability and availability. In essence, RCM embodies a shift from a reactive, one-size-fits-all approach to maintenance towards a proactive, risk-based strategy that prioritizes resources where they are most impactful, thus optimizing system reliability and minimizing downtime.
Why RCM Matters in Control Systems:
In industries where precision and reliability are paramount, such as manufacturing, aerospace, automotive, and energy, control systems serve as the backbone of critical processes and operations. In these sectors, even the slightest deviation from optimal performance can have far-reaching consequences, ranging from production delays and increased costs to safety hazards and reputational damage. Recognizing the significance of uninterrupted operation, Reliability-Centered Maintenance (RCM) emerges as a cornerstone approach to safeguarding system reliability and minimizing downtime. Unlike conventional maintenance strategies that rely on predefined schedules or reactive responses to failures, RCM adopts a proactive stance by systematically identifying potential failure modes, assessing their consequences, and devising targeted maintenance actions to mitigate associated risks. This methodical approach allows industries to address vulnerabilities in control systems before they escalate into unexpected breakdowns, thereby enhancing system availability and reliability.
One of the primary strengths of RCM lies in its ability to tailor maintenance activities to the specific needs and criticality of individual components within a control system. By prioritizing resources towards the most crucial elements based on their impact on system performance and safety, RCM optimizes the allocation of maintenance efforts and resources. This targeted approach not only minimizes unnecessary maintenance tasks but also ensures that critical components receive the attention and care they require to operate at peak efficiency. Moreover, by leveraging advanced analytical techniques and reliability data, RCM enables industries to make informed decisions regarding maintenance intervals, strategies, and resource allocation. This data-driven approach not only maximizes the effectiveness of maintenance activities but also minimizes the risk of over-maintenance or under-maintenance, both of which can compromise system reliability.
Furthermore, in dynamic industrial environments where control systems are subjected to evolving operating conditions and stressors, RCM provides a framework for adapting maintenance strategies in real-time. By continuously monitoring system performance, analyzing failure trends, and updating maintenance plans accordingly, industries can effectively manage risks and maintain system reliability over the long term. Additionally, RCM aligns with the broader goals of asset management and operational excellence, contributing to improved productivity, cost savings, and regulatory compliance.
In conclusion, in industries where precision, reliability, and uptime are critical, such as manufacturing, aerospace, automotive, and energy, Reliability-Centered Maintenance plays a pivotal role in ensuring uninterrupted performance of control systems. By proactively identifying and addressing potential failure modes, optimizing maintenance activities, and adapting strategies in response to changing conditions, RCM enhances system availability, reliability, and overall operational efficiency.
The Role of MATLAB in RCM for Control Systems:
MATLAB stands out as a cornerstone in the realm of engineering for its multifaceted capabilities in modeling, simulation, and analysis, providing an indispensable toolkit for engineers seeking to implement Reliability-Centered Maintenance (RCM) strategies in control systems. Its comprehensive suite of tools empowers engineers to delve deep into system reliability through meticulous analysis, enabling the identification of potential failure modes and the assessment of their consequences. With MATLAB's robust functionalities, engineers can conduct reliability analyses that span various statistical methods, estimating failure rates and predicting component lifetimes with precision. Moreover, MATLAB facilitates the optimization of maintenance schedules by seamlessly integrating reliability data with cost analysis, enabling engineers to strike a delicate balance between minimizing downtime and maximizing system reliability. The platform's predictive maintenance capabilities are equally compelling, allowing engineers to develop sophisticated algorithms based on real-time sensor data, thereby preemptively addressing potential failures before they impact system performance. MATLAB's role extends further into risk assessment, enabling engineers to simulate and analyze different failure scenarios to inform proactive maintenance plans effectively. In essence, MATLAB emerges as a pivotal asset for engineers navigating the complexities of RCM in control systems, offering unparalleled support across the spectrum of reliability analysis, predictive maintenance, and optimization endeavors. Leveraging MATLAB's capabilities, engineers can:
- Perform reliability analysis: MATLAB's statistical and reliability analysis functions empower engineers to comprehensively evaluate the reliability and failure attributes of control system components. Through the analysis of failure data, engineers can discern patterns and trends, enabling accurate estimation of failure rates. Furthermore, MATLAB facilitates the prediction of component lifetimes by employing advanced modeling techniques. This robust toolkit equips engineers with essential insights into the performance and longevity of control system elements, enabling informed decision-making and proactive maintenance strategies to ensure optimal system reliability and functionality.
- Optimize maintenance schedules: Integrating reliability data with maintenance cost analysis in MATLAB enables engineers to optimize maintenance schedules for control systems. By leveraging this integration, engineers can determine the most cost-effective maintenance intervals and strategies that effectively balance system reliability and downtime. MATLAB's analytical capabilities allow for a thorough examination of failure probabilities, component lifetimes, and associated maintenance costs, empowering engineers to make informed decisions. This approach ensures that maintenance efforts are strategically allocated, minimizing operational disruptions while maximizing the overall reliability and performance of control systems.
- Implement predictive maintenance: MATLAB's predictive modeling capabilities empower engineers to create algorithms that forecast equipment failures using real-time sensor data. By discerning early warning signs of potential malfunctions, predictive maintenance proactively tackles issues before they escalate, bolstering system reliability. This preemptive approach not only minimizes downtime but also optimizes maintenance efforts, ensuring the smooth operation of control systems across various industries.
- Perform risk assessment: MATLAB empowers engineers to conduct risk assessments by simulating diverse failure scenarios and their potential impact on system performance. This functionality allows for informed decision-making regarding maintenance priorities and resource allocation, ensuring that the most critical risks are effectively mitigated. By accurately modeling various failure scenarios, engineers can assess the probability and severity of potential failures, enabling proactive maintenance strategies that minimize downtime and maximize system reliability. This capability not only enhances operational efficiency but also optimizes resource utilization, ultimately contributing to the overall robustness and longevity of control systems across diverse industries.
Conclusion:
In conclusion, Reliability-Centered Maintenance (RCM) stands as a cornerstone for ensuring the sustained peak performance and durability of control systems across a multitude of industries. Its systematic approach to maintenance planning and decision-making, prioritizing resources towards critical components, is paramount in today's dynamic operational environments. However, the efficacy of RCM is significantly amplified when coupled with the formidable capabilities of MATLAB. Serving as a robust toolkit, MATLAB empowers engineers with a suite of tools and functionalities essential for the seamless implementation of RCM strategies. Through MATLAB, engineers gain the ability to meticulously assess the reliability of control system components, employing statistical and reliability analysis functions to decipher failure characteristics and estimate lifetimes accurately. This insight allows for the optimization of maintenance schedules, a critical aspect of RCM, where MATLAB's integration of reliability data with cost analysis facilitates the determination of cost-effective maintenance intervals that minimize downtime while maximizing system reliability.
Moreover, MATLAB facilitates the implementation of predictive maintenance, a proactive approach crucial for preemptively addressing potential failures. By leveraging MATLAB's predictive modeling capabilities, engineers can develop sophisticated algorithms that analyze real-time sensor data to identify early indicators of impending failures, enabling timely intervention and maintenance. Additionally, MATLAB serves as a powerful tool for conducting risk assessments, allowing engineers to simulate the impact of various failure scenarios on system performance comprehensively. This capability empowers decision-makers to prioritize maintenance activities and allocate resources efficiently, mitigating the most critical risks and bolstering overall system reliability.
By harnessing MATLAB's capabilities, engineers can elevate control system reliability to unprecedented levels, significantly minimizing downtime and optimizing operational efficiency. Whether in manufacturing, aerospace, automotive, or energy sectors, MATLAB's prowess as a toolkit for implementing RCM strategies transcends industry boundaries, providing engineers with a versatile platform to address the unique challenges of each domain. In essence, the symbiotic relationship between RCM and MATLAB epitomizes a paradigm shift in maintenance practices, where data-driven insights and proactive strategies converge to safeguard control systems' optimal functionality and longevity amidst the ever-evolving industrial landscape. In this context, MATLAB emerges not just as a software tool but as an indispensable ally for engineers striving to navigate the complexities of modern control systems and uphold their reliability in the face of myriad operational demands.