A Comprehensive Overview of PID Controller Design Using MATLAB
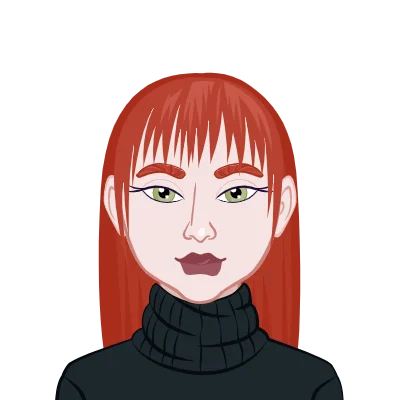
PID (Proportional-Integral-Derivative) controllers are widely used in control systems to regulate and stabilize various processes. They are essential components in fields ranging from engineering to industrial automation. In this theoretical discussion, we will explore the fundamental concepts behind PID controllers and understand how to solve your PID controller design assignment using MATLAB, keeping the focus on the theoretical aspects to help university students gain a strong grasp of the subject.
The Basics of PID Control
Proportional (P) Term
The proportional term in a PID controller responds directly to the current error, which is the difference between the desired setpoint and the current process variable. It amplifies this error by a factor known as the proportional gain (Kp). The proportional term's function is to bring the system's output closer to the desired setpoint.
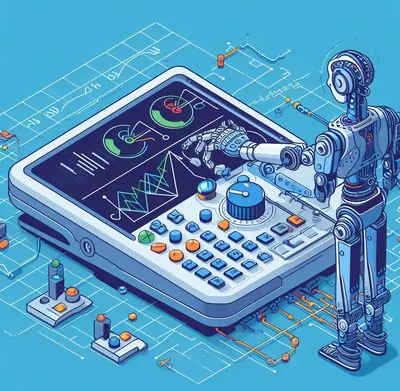
The control action generated by the proportional term is given by:
P(t)=Kp⋅e(t)
Where:
P(t) is the proportional control action.
Kp is the proportional gain.
e(t) is the error at time t.
A higher Kp value makes the controller more aggressive in reducing the error, but it can lead to overshoot and oscillations.
Integral (I) Term
The integral term in a PID controller addresses the accumulation of past errors over time. It is crucial for eliminating steady-state error, which occurs when the system doesn't reach and maintain the desired setpoint. The integral term is proportional to the integral of the error concerning time and is controlled by the integral gain (Ki).
The control action generated by the integral term is given by:
I(t)=Ki⋅∫_0^t e(τ)dτ
Where:
I(t) is the integral control action.
Ki is the integral gain.
e(τ) is the error at time τ, integrated from the beginning (0) to time t.
A higher Ki value increases the controller's ability to eliminate steady-state error but may lead to instability if set too high.
Derivative (D) Term
The derivative term in a PID controller anticipates future error by considering the rate of change of the error. It is controlled by the derivative gain (Kd). The derivative term helps reduce overshoot and dampen the system's response.
The control action generated by the derivative term is given by:
D(t)=Kd⋅d/dte(t)
Where:
D(t) is the derivative control action.
Kd is the derivative gain.
d/dte(t) is the rate of change of the error concerning time.
A higher Kd value increases the damping effect and reduces overshoot but can make the system more sensitive to noise.
PID Controller Transfer Function
Mathematically, the PID controller can be represented by its transfer function:
Gc(s)=Kp+Ki/s+Kds
Where:
Gc(s) is the transfer function of the PID controller.
Kp,Ki, and Kd are the proportional, integral, and derivative gains, respectively.
s is the Laplace variable representing the frequency domain.
The transfer function Gc(s) describes how the PID controller manipulates the error signal e(t) to produce the control output u(t).
MATLAB for PID Controller Design
MATLAB, a powerful software platform, provides a convenient environment for designing and analyzing PID controllers. University students can leverage MATLAB's capabilities for control system design and analysis. Here's a high-level overview of the steps involved in designing a PID controller using MATLAB:
- Define the Plant Transfer Function:
- Choose PID Controller Parameters:
- Performance Criteria: Define specific performance criteria for the control system, such as settling time, overshoot, and steady-state error. These criteria guide the selection of PID parameters.
- Tuning Methods: Employ tuning methods like Ziegler-Nichols or Cohen-Coon (as discussed earlier) to estimate initial PID parameter values. These methods provide starting points for tuning.
- Simulation: Use simulation tools in MATLAB to assess the system's response with different PID parameter values. This iterative process helps refine the parameter selection.
- Create the PID Controller in MATLAB:
- Connect the Controller and Plant:
- Closed-Loop System Simulation:
Before diving into PID controller design, it is essential to have a mathematical model that represents the plant or system you intend to control. This model characterizes the behaviour of the system and is typically represented as a transfer function.
A transfer function is a mathematical representation of the system's input-output relationship in the frequency domain. It describes how the system responds to changes in the input signal. Transfer functions are essential in control system analysis and design as they provide insights into system dynamics.
In MATLAB, you can define the plant transfer function using the Control System Toolbox. This typically involves specifying the numerator and denominator coefficients of the transfer function that accurately represents the system under consideration.
Selecting suitable values for the PID controller parameters, namely the proportional gain (Kp), integral gain (Ki), and derivative gain (Kd), is a crucial step in controller design. The choice of these parameters significantly affects the system's performance, stability, and response.
To determine the appropriate PID parameters:
System Characteristics: Understand the inherent characteristics of the system, such as its time constant, natural frequency, and damping ratio. This knowledge helps in choosing initial values for the gains.
Once you have determined the PID controller parameters, you can create a PID controller object in MATLAB using the Control System Toolbox. MATLAB provides a straightforward way to define a PID controller with the specified gains.
You can customize the PID controller object to suit your specific needs, such as configuring anti-windup mechanisms, specifying output limits, or setting the sample time for digital control systems.
In control system design, the PID controller is typically connected to the plant model in a closed-loop configuration. This connection creates a feedback control system where the controller continuously adjusts the plant's input based on the measured output and the desired setpoint.
In MATLAB, you can connect the PID controller and plant model using appropriate functions and blocks, depending on your modelling approach (e.g., transfer function, state-space representation, or Simulink).
Simulation is a vital step in the design and analysis of control systems. MATLAB offers powerful simulation tools that allow students to study the closed-loop system's behaviour under various conditions. By applying different inputs and disturbances, students can analyze the system's transient and steady-state responses.
Simulation helps in assessing:
- System Stability: Determine whether the system is stable or prone to oscillations or divergence.
- Transient Response: Analyze how the system responds to changes in setpoints or external disturbances.
- Performance Metrics: Measure performance criteria like settling time, overshoot, and steady-state error to assess how well the system meets the desired objectives.
6. Fine-Tuning:
The final step in PID controller design is fine-tuning. This is an iterative process where students adjust the controller parameters to achieve the desired performance characteristics. MATLAB's simulation capabilities make it easy to experiment with different parameter values and observe their effects on system behaviour.
During fine-tuning, students can:
- Optimize Performance: Fine-tune the PID parameters to minimize overshoot, reduce settling time, and minimize steady-state error while maintaining system stability.
- Robustness Analysis: Assess the system's robustness to variations in the plant's parameters or external disturbances.
- Anti-Windup and Saturation: If necessary, implement anti-windup mechanisms or address control signal saturation issues to improve controller performance.
By iteratively adjusting and simulating the controller parameters, students gain valuable insights into the trade-offs involved in control system design and develop the skills to optimize PID controllers for real-world applications.
Practical Tips for PID Controller Design
Choosing PID Controller Parameters
Selecting appropriate PID controller parameters Kp,Ki, and Kd is a crucial step in controller design. Here are practical tips:
- Proportional Gain (Kp): A higher Kp value results in a stronger response to errors, but it can lead to overshoot and instability. Lower values can reduce overshoot but may increase settling time.
- Integral Gain (Ki): Ki helps eliminate steady-state error. Increasing Ki reduces steady-state error, but excessively high values can cause instability and oscillations.
- Derivative Gain (Kd): Kd is essential for dampening the response and reducing overshoot. Higher Kd values enhance stability but can amplify noise if set too high.
Tuning Methods
Several tuning methods are available to help determine suitable PID parameters:
- Ziegler-Nichols Method: This heuristic method involves step-testing the system and using specific rules to estimate PID gains. It's a good starting point for tuning.
- Cohen-Coon Method: Another heuristic approach that provides approximate PID tuning values based on system characteristics. It's useful for quick initial tuning.
- Model-Based Methods: These advanced methods use mathematical models of the plant to optimize PID parameters. They provide more precise tuning but require a good understanding of the system's dynamics.
Conclusion
PID controllers play a pivotal role in control systems, and MATLAB serves as a valuable tool for their design and analysis. This theoretical discussion has provided university students with a comprehensive understanding of PID controller principles and their implementation using MATLAB. By grasping the theoretical concepts and utilizing MATLAB's capabilities, students can excel in assignments and courses related to control systems engineering. Moreover, students can utilize the help of professional MATLAB assignment experts especially when encountering an urgent assignment. Remember that PID controller design is both a science and an art, requiring practice and experimentation to achieve optimal results.