PID Controller for Temperature Control in Industrial Process
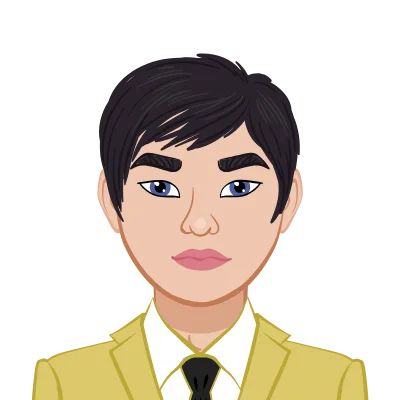
Transfer Function-Based Modeling
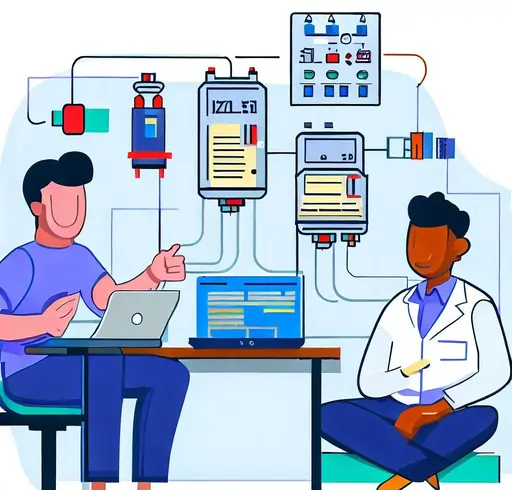
Understand the concept of transfer function-based modeling before delving into the design and implementation of the PID controller. This is an essential step before getting into the design and implementation of the PID controller. Within the context of the frequency domain, the connection that exists between a system's inputs and outputs is denoted by a transfer function. When it comes to the regulation of temperatures, the transfer function establishes a connection between the input temperature set point and the temperature measured by the system.
The first thing that needs to be done in order to build a transfer function model for the temperature control system is to collect data from experiments. This data typically consists of input-output pairs that were obtained by making use of a known input (for example, making a step change in the setpoint temperature) and recording the corresponding output temperature response. Using system identification techniques such as the Least Squares Method or the Instrumental Variable Method, one can derive a transfer function model by analyzing these data first. One of these methods is called the Instrumental Variable Method. Remember to prioritize and complete your transfer function assignment in order to enhance your understanding of the topic.PID Controller Design
When we have the system's transfer function model in hand, we can move on to the next step of the process, which is designing the PID controller. PID stands for proportional, integral, and derivative, and it refers to the three parts that make up the controller. The overall control action is improved in a particular way thanks to the contributions made by each individual component. The output that is provided by the proportional component is proportional to the difference between the temperature set point and the temperature that was actually measured. It helps to reduce the error in the steady-state value, but it does not take into account the dynamics of the system. The error is integrated over time by the integral component, which results in a reduction in the cumulative error. It contributes to the elimination of the steady-state error and enhances the system's response to changes in the set point. The derivative component computes the rate of change of the error and then provides a control action that is based on the rate at which the error is changing. This component is responsible for predicting how the system will behave, which contributes to the reduction of overshoot and the improvement of stability. These three components are brought together by the PID controller to produce a control signal that minimizes the difference between the set point temperature and the actual temperature. This results in effective temperature control.
MATLAB Implementation
The PID controller design and implementation processes can be made easier with the help of MATLAB's robust environment. Take the following steps in order to successfully implement the PID controller for temperature control: Define the transfer function model that was obtained by using the tf function in MATLAB to complete the system identification process. Utilize the petune function in order to automatically tune the PID controller parameters according to the desired control performance specifications. Some examples of these specifications include settling time, overshoot, and integral of the absolute error. Adjust the PID controller parameters manually based on how the system reacts to incremental shifts in the set point if you would rather tune the system manually rather than automatically. Using the feedback function, you can make a feedback control loop that will connect the PID controller to the transfer function model. Use the sim function to perform a simulation of the closed-loop system, passing in the set point trajectory as well as the initial conditions. Utilizing the plotting capabilities provided by MATLAB, conduct an analysis of the system's response by plotting the set point, the measured temperature, and the control signal. Students will be able to gain hands-on experience in designing and implementing a PID controller for temperature control in an industrial process if they follow these steps and follow the instructions carefully. Because of its extensive library of functions and its powerful visualization capabilities, MATLAB is an excellent instrument for researching and evaluating control systems.
Controller Tuning Methods
After the PID controller has been designed, the next critical step is to tune the controller's parameters in order to achieve the highest possible level of control performance. Adjusting the proportional, integral, and derivative gains of the controller in order to achieve the desired behavior of the system is what is meant by the term "tuning." There are a few different approaches to tuning, each of which comes with its own set of benefits and potential drawbacks.
- The Ziegler-Nichols Method: The Ziegler-Nichols method is a well-known tuning method that is based on step response analysis. Increasing the proportional gain up to the point where the system demonstrates sustained oscillations is what this method entails. Using empirical formulas, one can figure out the proportional, integral, and derivative gains based on the ultimate gain and the oscillation period. The implementation of this method is fairly straightforward, but it could result in overshoot and slow response times.
- The Cohen-Coon Method: The Cohen-Coon method is another frequently used tuning method that also relies on step response analysis. It is very similar to the Ziegler-Nichols method in that it requires determining the ultimate gain as well as the ultimate period. However, the proportional, integral, and derivative gains are all calculated using different empirical formulas, which results in a somewhat unique response. When compared to the Ziegler-Nichols method, the Cohen-Coon method frequently offers a more satisfactory equilibrium between the system's stability and its performance.
- Methods That Are Model-Based: In model-based methods, the optimal controller parameters are determined by applying the mathematical model of the system to the problem at hand. Estimating the dynamics of the process, such as its time constants and gains, is a common step in these methods. Additionally, optimization algorithms are utilized in order to determine the optimal PID parameter values. Model-based methods require a solid comprehension of the mathematical model of the system in order to produce more accurate tuning results. However, these methods can provide more precise tuning outcomes.
Selecting the appropriate tuning method depends on the specific requirements of the temperature control system and the desired control performance. Students studying in universities can experiment with different tuning methods using MATLAB and compare the results to gain a deeper understanding of the tuning process.
Performance Evaluation Metrics
To determine whether or not a PID controller is efficient at maintaining a desired temperature, it is necessary to evaluate the controller's performance. Quantifying the performance of the controller and contrasting the effectiveness of various control strategies can be done with the help of a number of different performance evaluation metrics.
The following are some metrics that are frequently used:
- Settling Time: The amount of time required for the system's response to reach and remain within a specified error range around the set point temperature is referred to as the settling time. When compared to longer settling times, faster response times indicate better control performance.
- Overshoot: Overshoot is the term used to describe the maximum deviation of the system's response from the temperature that was set point. In an ideal situation, a properly tuned PID controller should minimize overshoot in order to prevent temperature fluctuations and instability.
- Rise Time: Rise time is the amount of time required for the system's response to transition from the initial state to a specified percentage (typically 90% or 95%) of the final value. A quicker response and improved control performance are both indicated by a shorter rise time.
- Integral of the Absolute Error (IAE): IAE is a cumulative measure of the absolute value of the error that has been occurring between the set point and the actual temperature over time. If the IAE can be made as small as possible, this indicates that the steady-state error has been minimized and the control performance has been improved.
Students can use these performance evaluation metrics in their MATLAB projects to compare different tuning methods, evaluate the impact of PID parameter settings on system behavior, and optimize the control strategy for temperature control.
Advanced Control Techniques
PID control is effective and widely used in a variety of industrial applications; however, there are advanced control techniques that offer improved performance and robustness. PID control is one such technique. Students who are interested in gaining a more in-depth comprehension of control systems should consider investigating these methods. The following are two sophisticated methods of control:
- Model Predictive Control (MPC): MPC is a sophisticated control technique that makes use of a dynamic model of the system in order to predict the behavior of the system and optimize the control action. MPC was developed by NASA in the 1960s. In order to provide optimal control, MPC takes into account the system's constraints, as well as future set point trajectories and disturbance rejection. It is especially helpful for systems with complex dynamics or multiple inputs and outputs, but it can be used in either case.
- Adaptive Control: Adaptive control is a method that adjusts the controller parameters based on the changing dynamics of the system. Adaptive control is a technique. It does this by continuously monitoring the behavior of the system and making adjustments to the PID gains in order to accommodate varying conditions of the process. Systems that have parameters that change over time or dynamics that are difficult to predict can benefit from adaptive control.
Students can broaden their knowledge and investigate the possibility of further improving temperature control in industrial processes by studying these advanced control techniques. PID control is a great place to begin, but students who understand more advanced techniques will be better prepared to tackle difficult control problems in their future careers.
Robustness and Stability Analysis
Controlling the temperature in industrial processes in a reliable and safe manner requires, first and foremost, that the PID controller be as robust and stable as possible. The ability of the controller to continue delivering satisfactory results despite the presence of certain unknowns or changes in the system is referred to as its robustness. The ability of the controller to keep oscillations bounded and to prevent system instability is what we mean when we talk about stability. Techniques for analyzing robustness and stability help evaluate and improve the controller's performance in a variety of different types of operating conditions.
- Gain and Phase Margin Analysis : Gain and phase margin analysis is a common method used to evaluate the stability and robustness of control systems. This analysis looks at the difference between the gain and phase margins. In order to determine the stability margins of the system, it is necessary to measure the gain margins and phase margins of the open-loop transfer function. Greater stability and robustness in the face of variations in the system can be inferred from the presence of a large gain margin and phase margin. Students have the ability to use MATLAB to analyses the gain and phase margins of the PID-controlled system and to make adjustments to ensure stability and robustness in their designs.
- Analysis of Bode Plots: The analysis of bode plots is yet another method that can be utilized to investigate the frequency response of the system. Through the examination of the gain and phase characteristics at a variety of frequencies, it offers extremely helpful insights into the stability and robustness of the system. Students are able to identify critical frequencies where the gain or phase margins are low and take corrective actions to improve stability and robustness if they plot the Bode diagram of the open-loop transfer function. This allows students to improve the system's stability and robustness.
Students are able to obtain a more in-depth understanding of the performance limitations and potential vulnerabilities of the PID controller through the use of analysis techniques that focus on robustness and stability. Students can explore strategies to improve the stability and robustness of temperature control systems by incorporating these analyses into their MATLAB assignments. This ensures that the systems will function in a reliable and safe manner when they are applied to real-world industrial applications.
Practical Considerations and Challenges
When attempting to control the temperature of an industrial process with a PID controller, there are a number of practical considerations and challenges that must be overcome. Students who have an understanding of these considerations are better able to anticipate and deal with potential problems that may arise during the process of implementation.
The following are some practical considerations and challenges that need to be taken into account:
- Appropriate Temperature Sensor: Selecting an Appropriate Temperature Sensor and Ensuring Its Proper Placement in the Process In order to obtain accurate temperature readings, it is essential to select an appropriate temperature sensor and ensure that its proper place in the process is maintained. When selecting a sensor, it is necessary to take into consideration a number of different factors, including response time, accuracy, and the conditions of the surrounding environment. Measurement errors can be introduced as a result of improper sensor selection or placement, which can also affect the PID controller's overall performance.
- Actuator Dynamics: The dynamics of the actuator, such as valves or heating elements, play a significant role in the overall response of the temperature control system. Actuators may have limitations, such as slow response times or non-linear behavior, which can affect the performance of the control. Students need to take into consideration the dynamics of the actuator and account for them during the process of controller design and tuning.
- Non-linearity and Disturbances: Non-linearity and Disturbances Industrial processes frequently exhibit non-linear behavior, and disturbances can have an effect on the temperature control. Changes in the properties of the material, the characteristics of the heat transfer, or the dynamics of the process can all result in non-linarites. Students need to be aware of the non-linearity and disturbances mentioned, and they should take them into consideration when designing a PID controller or investigating advanced control techniques.
- Interaction with Other Control Loops: In sophisticated industrial systems, temperature control is frequently just one component of a larger control scheme that consists of multiple interconnected control loops. Students need to have an understanding of how the temperature control loop interacts with other control loops to ensure proper coordination and avoid conflicts or instability.
Conclusion
In this blog, we have discussed the design and implementation of a PID controller for temperature control in an industrial process by using transfer function-based modeling. This was done so as to keep the temperature at the desired level. During our conversation, we went over the significance of transfer function modeling and the functions that each component serves in the PID controller. Because we also included detailed instructions on how to implement the controller by making use of MATLAB, this article can serve as an invaluable resource for students currently enrolled in university programmers who are completing MATLAB-related coursework. Students will be equipped with essential skills for addressing real-world control challenges in a variety of industries if they have a fundamental understanding of the principles underlying PID control and gain hands-on experience putting those principles into practice using MATLAB. Industries that are able to optimize their temperature control can improve product quality while simultaneously lowering their overall energy consumption and boosting their overall operational efficiency.