Solving Inverse Kinematics Problems with Simulink: Robotics Assignments

Inverse kinematics is a fundamental concept in the field of robotics, serving as a pivotal tool for determining the joint configurations necessary to achieve a desired end-effector position and orientation. Unlike forward kinematics, which involves predicting the position of the end-effector based on known joint angles, inverse kinematics deals with the reverse process, enabling robots to plan their movements effectively in real-world scenarios. This concept is crucial in robotics as it allows for precise control and manipulation of robotic arms, enabling them to perform complex tasks such as reaching a specific point in space or following a desired trajectory. Inverse kinematics forms the backbone of various robotic applications, including industrial automation, medical robotics, and autonomous vehicles, where precise motion planning is essential for successful operation.
The importance of solving inverse problems in Simulink assignments cannot be overstated, particularly in educational settings where students are tasked with understanding and implementing advanced robotic control techniques. By mastering inverse kinematics, students gain a deeper understanding of robot kinematics and dynamics, which are essential for designing and programming robotic systems. Moreover, inverse kinematics problems serve as practical exercises that challenge students to apply theoretical concepts in real-world scenarios, fostering critical thinking and problem-solving skills essential for success in the field of robotics. Proficiency in solving inverse kinematics problems not only enhances students' academic performance but also prepares them for careers in robotics engineering and related fields.
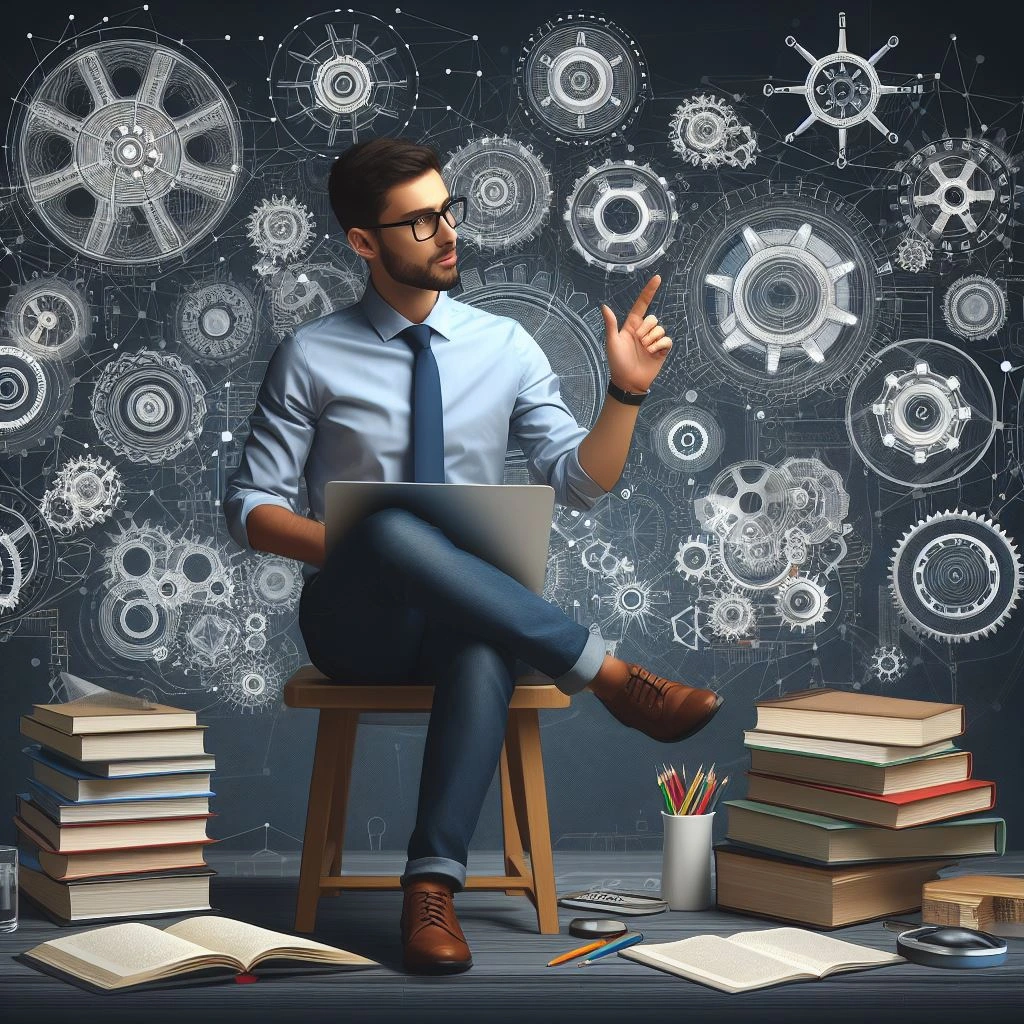
Simulink, a powerful simulation and modeling environment provided by MATLAB, emerges as a valuable tool for addressing the challenges associated with solving inverse kinematics problems in robotics assignments. Simulink offers a user-friendly interface equipped with a vast array of tools and functionalities specifically designed for modeling and simulating dynamic systems, making it an ideal platform for implementing and testing robotic control algorithms. Its intuitive graphical interface allows students to visualize and simulate complex robotic systems, facilitating the analysis and optimization of inverse kinematics solutions. Additionally, Simulink provides access to various built-in libraries and blocks tailored for robotics applications, enabling students to quickly prototype and iterate their designs. Furthermore, Simulink's integration with MATLAB allows for seamless integration with other MATLAB toolboxes, such as Robotics System Toolbox, providing access to additional functionalities for robotic control and simulation. Overall, Simulink serves as a comprehensive solution for students seeking assistance with Simulink assignment related to inverse kinematics in robotics, offering a versatile platform for exploring and implementing advanced robotic control techniques.
Understanding Inverse Kinematics:
Inverse kinematics is a crucial concept in robotics that involves determining the joint configurations of a robotic manipulator to achieve a desired end-effector position and orientation. Unlike forward kinematics, which calculates the end-effector pose based on known joint angles, inverse kinematics works in the opposite direction, figuring out the joint angles required to reach a specific end-effector pose. This process is essential in robotics because it enables precise control of robotic manipulators, allowing them to perform tasks with accuracy and efficiency.
In real-world applications, inverse kinematics plays a vital role across various industries and domains where robotic manipulators are utilized. One prominent example is in industrial automation, where robots are deployed for tasks such as pick-and-place operations, assembly line tasks, and welding. In these scenarios, robots need to precisely position their end-effectors to manipulate objects or perform specific actions. Inverse kinematics algorithms enable robots to calculate the joint angles required to achieve the desired end-effector positions, facilitating precise and reliable automation processes in manufacturing environments.
Another significant application of inverse kinematics is in the field of robotics surgery. Surgical robots are increasingly used in minimally invasive procedures where precise movements are essential to ensure the safety and success of the operation. For instance, in laparoscopic surgery, where instruments are inserted through small incisions in the patient's body, robotic manipulators must navigate tight spaces and manipulate tools with utmost accuracy. Inverse kinematics algorithms enable surgical robots to calculate the joint angles needed to navigate the instruments inside the body and perform intricate surgical tasks with precision, reducing the risk to patients and improving surgical outcomes.
In the domain of animation and virtual reality, inverse kinematics is also extensively used to create lifelike movements of virtual characters or avatars. Video game developers, filmmakers, and animators leverage inverse kinematics algorithms to animate characters' movements realistically, ensuring that they interact with their environment and perform actions naturally. Whether it's a character picking up an object, walking, or performing complex gestures, inverse kinematics enables the seamless animation of movements, enhancing the immersion and realism of virtual worlds and entertainment experiences.
Overall, inverse kinematics is a fundamental concept in robotics with widespread applications across industries such as manufacturing, healthcare, entertainment, and beyond. Its ability to calculate precise joint configurations for robotic manipulators enables a wide range of tasks, from industrial automation and surgical procedures to animation and virtual reality, contributing to advancements in technology and improving various aspects of human life.
Overview of Simulink:
Simulink is a graphical programming environment within MATLAB, designed specifically for modeling, simulating, and analyzing dynamic systems. Its intuitive graphical interface allows engineers and researchers to visually represent and simulate complex systems using blocks and connections, making it an indispensable tool in various engineering disciplines.
At its core, Simulink leverages MATLAB's computational power and extensive mathematical libraries, enabling users to seamlessly integrate control systems, signal processing algorithms, and physical models into a unified simulation environment. This integration between MATLAB and Simulink streamlines the design process, allowing engineers to prototype and iterate on their designs rapidly.
One of the primary advantages of using Simulink is its ability to tackle complex engineering problems efficiently. By providing a visual representation of systems and their interactions, Simulink enables engineers to gain insights into system behavior and performance quickly. This visual representation also facilitates collaboration among team members, as it offers a clear and intuitive way to communicate design ideas and concepts.
Moreover, Simulink offers a wide range of pre-built blocks and libraries covering various domains such as control systems, signal processing, communications, and more. These built-in blocks, along with customizable components, significantly accelerate the development process, reducing time-to-market for engineering solutions.
Another key advantage of Simulink is its support for multi-domain modeling. Engineers can seamlessly integrate different physical domains, such as mechanical, electrical, and hydraulic systems, within a single simulation environment. This capability is particularly valuable in the field of robotics, where complex interactions between mechanical components, sensors, and control algorithms need to be accurately modeled and simulated.
Furthermore, Simulink provides extensive analysis and visualization tools, allowing engineers to validate and optimize their designs effectively. From time-domain simulations to frequency-domain analysis and sensitivity studies, Simulink offers a comprehensive suite of tools for analyzing system performance and behavior under various conditions.
In summary, Simulink plays a crucial role in MATLAB by providing a powerful and intuitive platform for modeling, simulating, and analyzing complex engineering systems. Its graphical interface, extensive library of pre-built blocks, support for multi-domain modeling, and analysis tools make it an invaluable tool for engineers and researchers working on a wide range of engineering problems, including those in robotics, control systems, signal processing, and beyond.
Setting Up the Simulink Model:
Setting up a Simulink model for solving inverse kinematics problems involves several key steps that harness Simulink's powerful capabilities within the MATLAB environment. To begin, ensure you have MATLAB and Simulink installed on your system. Once ready, follow these steps:
Firstly, launch MATLAB and open Simulink by typing "simulink" in the MATLAB command window. This action opens the Simulink Library Browser, where you'll find various blocks and tools for building your model.
Next, define the components of your robotic system within the Simulink environment. This includes specifying the robot's kinematic structure, such as the number of joints and their respective ranges of motion. Utilize Simulink's various block libraries, including the Simscape Multibody library, to represent the robot's physical components accurately.
After defining the robotic system, incorporate the mathematical model for solving inverse kinematics. Depending on the complexity of your robot and its kinematic structure, this may involve implementing analytical or numerical methods. For analytical methods, you can use Simulink's mathematical blocks to represent equations governing the robot's motion. For numerical methods, consider utilizing MATLAB functions within Simulink to perform iterative calculations.
Once the mathematical model is incorporated, establish input signals representing the desired end-effector positions or trajectories. These signals drive the inverse kinematics solver to compute the corresponding joint configurations required to achieve the desired end-effector motion. Simulink provides various signal sources and generators to define these input signals, such as the Step block for step inputs or the Sinusoidal block for periodic trajectories.
Connect the input signals to the inverse kinematics solver within your Simulink model. This connection allows the solver to receive the desired end-effector positions or trajectories as input and compute the corresponding joint configurations. Use Simulink's signal routing and connection tools to establish these connections effectively.
Finally, configure the simulation settings and run the Simulink model to solve the inverse kinematics problem. Specify the simulation time and any additional parameters relevant to your robotic system. Once configured, initiate the simulation to observe the computed joint configurations over time in response to the specified end-effector motion.
Throughout this process, leverage Simulink's visual interface to build and visualize your robotic system's model effectively. Use screenshots or code snippets to illustrate each step, providing readers with a clear and comprehensive guide to setting up a Simulink model for solving inverse kinematics problems.
Solving Inverse Kinematics with Simulink:
In Simulink, solving inverse kinematics (IK) problems for robotics applications entails utilizing various methods and techniques tailored to specific robotic systems and tasks. One prominent approach involves using Simulink's built-in blocks to formulate and solve IK equations numerically. These blocks enable users to define the robot's kinematic structure, input desired end-effector positions, and compute the corresponding joint configurations. For instance, employing the "Inverse Kinematics Solver" block allows users to specify the desired end-effector pose and constraints, such as joint limits or collision avoidance, to compute feasible joint angles. This method is particularly useful for manipulator arms with articulated joints, where analytical solutions may be challenging to derive due to complex kinematic structures or external constraints.
Another method involves implementing custom IK algorithms within Simulink using MATLAB Function blocks or Simulink Function blocks. This approach provides flexibility in designing IK algorithms tailored to specific robotic systems or tasks. For example, users can develop iterative numerical methods like the Jacobian-based IK solver or gradient descent algorithms to iteratively adjust joint angles until the desired end-effector pose is achieved. By encapsulating custom IK algorithms within Simulink blocks, users can seamlessly integrate them into larger robotic control systems and leverage Simulink's simulation and visualization capabilities for validation and testing.
Furthermore, Simulink supports interfacing with external robotics libraries or toolboxes, such as Robotics System Toolbox, to access pre-built IK solvers or algorithms. These toolboxes offer a wide range of IK algorithms, including analytical, numerical, and optimization-based methods, which can be seamlessly integrated into Simulink models. For instance, users can leverage Robotics System Toolbox's "inverseKinematics" function to compute joint configurations for a given end-effector pose, taking into account robot kinematics, joint limits, and other constraints. This approach simplifies IK implementation by leveraging established algorithms and ensures compatibility with various robotic platforms supported by the toolbox.
To illustrate these methods, consider a robotic manipulator tasked with reaching a series of predefined target positions in a simulated environment. By employing Simulink's IK solver blocks or custom IK algorithms, the manipulator can dynamically adjust its joint angles to navigate to each target position accurately while respecting joint limits and avoiding collisions with obstacles. Additionally, integrating external IK solvers from Robotics System Toolbox enables seamless integration of advanced IK algorithms, such as closed-form solutions or numerical optimization methods, to achieve precise and efficient robotic motion planning. Through these examples, it's evident that Simulink offers a versatile platform for solving IK problems in robotics, accommodating diverse methods and facilitating seamless integration into larger control systems for real-world applications.
Tips and Best Practices:
Efficiently utilizing Simulink in robotics assignments requires a strategic approach and adherence to best practices. Firstly, it's crucial to familiarize oneself with Simulink's interface, understanding its blocks, libraries, and functionalities. This knowledge forms the foundation for building robust models. Secondly, organizing the Simulink model in a logical and modular fashion enhances clarity and simplifies troubleshooting. Utilizing subsystems and hierarchical structures helps manage complexity, allowing for easier navigation and modification.
Effective parameterization is another essential aspect. Assigning meaningful names to blocks and variables facilitates comprehension and documentation, streamlining collaboration and future modifications. Additionally, utilizing MATLAB functions within Simulink enables the integration of custom algorithms and enhances model flexibility.
When working on robotics assignments, challenges such as computational complexity and real-time constraints often arise. To mitigate these challenges, it's advisable to optimize the model by simplifying mathematical expressions, reducing unnecessary computations, and utilizing Simulink's built-in optimization tools. Moreover, leveraging Simulink's simulation capabilities enables thorough testing and validation of the model's behavior, ensuring its reliability in real-world scenarios.
Another common challenge is interfacing Simulink models with physical hardware. To overcome this, utilizing Simulink's support for hardware-in-the-loop (HIL) simulation facilitates seamless integration with hardware components, allowing for accurate performance evaluation and validation. Furthermore, utilizing Simulink's code generation capabilities enables the deployment of models to embedded systems, facilitating real-time control and implementation in robotic platforms.
Collaboration and version control are also vital aspects of efficient Simulink usage in robotics assignments. Utilizing version control systems such as Git enables team collaboration, tracks changes, and ensures the integrity of the model throughout its development lifecycle. Additionally, documenting the model thoroughly, including design decisions, assumptions, and validation results, enhances reproducibility and facilitates knowledge transfer within the team.
In conclusion, efficient utilization of Simulink in robotics assignments necessitates a systematic approach, adherence to best practices, and proactive management of common challenges. By mastering Simulink's interface, organizing models effectively, optimizing performance, leveraging simulation capabilities, interfacing with hardware, and facilitating collaboration and documentation, engineers can effectively address the complexities of robotics assignments and achieve robust and reliable solutions.
Conclusion:
In this blog post titled "Solving Inverse Kinematics Problems with Simulink: Robotics Assignments," we explored the fundamental concepts of inverse kinematics in robotics and how Simulink can be a powerful tool for addressing these challenges. We began by defining inverse kinematics and highlighting its significance in robotics, emphasizing its real-world applications across various industries. Simulink, a component of MATLAB, was introduced as a versatile platform for modeling, simulating, and analyzing dynamic systems, making it an ideal choice for tackling complex engineering problems like inverse kinematics.
We delved into the setup of a Simulink model for solving inverse kinematics problems, breaking down the process into manageable steps and providing visual aids to assist readers in understanding the implementation. Various methods and techniques available in Simulink for solving inverse kinematics problems were discussed, accompanied by examples and case studies to demonstrate their practical applications. Throughout the discussion, we shared tips and best practices for efficiently using Simulink in robotics assignments, addressing common challenges and providing strategies for overcoming them.
In conclusion, readers were encouraged to apply the knowledge gained from the blog post in their robotics assignments, emphasizing the practical relevance and applicability of the discussed concepts. By leveraging Simulink's capabilities, readers can enhance their understanding of inverse kinematics and develop effective solutions for robotics tasks. A call-to-action prompted readers to visit the website, matlabassignmentexperts.com, for additional MATLAB assignment help, particularly in the realm of robotics assignments. Finally, readers were invited to engage further by leaving comments and questions, fostering a sense of community and encouraging active participation in the discussion.
Overall, this blog post serves as a valuable resource for students and professionals alike, offering insights into solving inverse kinematics problems with Simulink and empowering readers to apply this knowledge in their robotics endeavors. Through practical examples, detailed explanations, and actionable tips, readers are equipped with the tools and understanding necessary to tackle complex robotics assignments effectively.