Achieving Precision and Stability with MATLAB Assignments on PID Controller Design
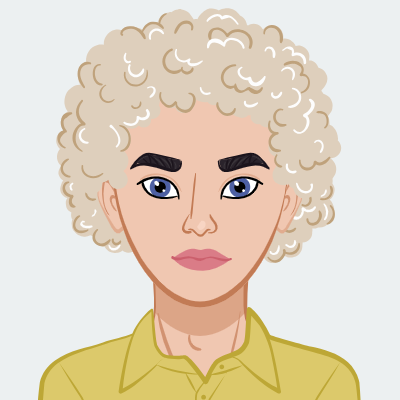
In engineering and industrial applications, the Proportional-Integral-Derivative (PID) controller is a popular control algorithm. This feedback control system calculates the difference between the intended setpoint and the actual output of the process or plant on a continuous basis. The system is then brought closer to the desired setpoint by the PID controller using proportional, integral, and derivative actions to modify the control signal.
PID controllers are widely used in many sectors, including process control, robotics, manufacturing, and aerospace. They are renowned for being straightforward, simple to use, and capable of delivering stability and effective performance in a variety of systems.
Understanding the PID Controller
The PID controller's proportional component is its most basic and easily understood component. The proportional gain (Kp), a constant factor, directly scales the error signal. The stronger the response to the error and the quicker the controller acts to reduce it, the higher the proportional gain.
High proportional gains can, however, also cause overshooting, oscillations, and system instability. On the other hand, a low proportional gain may cause a sluggish response and make it challenging to accurately track the setpoint. Finding the ideal balance is crucial when designing a PID controller.
Integral (I) Component
The integral component applies a correction to get rid of any steady-state errors in the system and accounts for the total sum of previous errors. When systematic biases or disturbances result in a constant offset between the setpoint and the process variable, the integral action is especially helpful.
How quickly the accumulated error affects the control signal depends on the integral gain (Ki). Integral windup may occur in the controller if the integral gain is set too high. When the integral term swells out of proportion, it causes the controller to overshoot or oscillate around the setpoint.
Derivative (D) Component
The derivative component accounts for the error's rate of change. It works to anticipate the error's future trend and temper the system's reaction to abrupt changes. The derivative action aids in reducing overshoot and stabilizing the system.
How fast the controller reacts to changes in the error depends on the derivative gain (Kd). A jittery and unstable response can result from the system's noise being amplified by a high derivative gain. In order to create a PID controller that is stable and effective, the derivative gain must be tuned.
Designing a PID Controller in MATLAB
A complete set of tools for designing and analyzing PID controllers is available in MATLAB. To complete MATLAB assignment on Control System Toolbox is specifically made to work with control systems, making it an effective environment for implementing PID controllers.
PID Controller Tuning
To achieve the desired system behavior, PID controller tuning entails choosing appropriate values for the proportional, integral, and derivative gains. There is no one-size-fits-all method for tuning a PID controller; instead, it depends on the characteristics of the particular system and the control goals.
PID controller tuning can be done in a number of ways, as was previously mentioned. The Ziegler-Nichols method, which involves exciting the system with a step input and then adjusting the gains in response to the system's response, is one well-liked technique. PID tuning can be automated using MATLAB's built-in pidTuner and pidtune functions, which can also be used to determine the best PID gains.
Simulink Implementation of PID Controller
Simulink, a graphical modeling and simulation environment from MATLAB, is frequently used for the design of control systems. The P, I, and D components, as well as their connections, are represented using blocks when creating a Simulink model for a PID controller.
The proportional, integral, and derivative components of the error signal can be calculated in Simulink, and they can then be combined to create the control signal. The control loop is then closed by sending the process variable back to the controller after the control signal has been applied to the plant.
You can analyze the PID controller's behavior in various scenarios by simulating the system's response to various inputs and disturbances using Simulink.
PID Autotuning
With the aid of the sophisticated technique known as PID autotuning, MATLAB is able to automatically modify the PID gains in response to the system's response. Autotuning is especially helpful when the system's parameters are ambiguous or dynamic.
The pidTuner and pidtune functions in MATLAB use optimization algorithms to identify the best PID gains that satisfy particular performance requirements. When manual tuning becomes difficult or time-consuming, these functions can be of great help.
Achieving Stability and Performance in Control Systems
The stability and robustness of a control system are strongly correlated with the phase and gain margins. The gain margin denotes the maximum additional gain that the system can tolerate, whereas the phase margin denotes the maximum additional phase shift that the system can tolerate before becoming unstable.
The phase and gain margins of a control system can be calculated using MATLAB's margin function. If a system has both a positive phase margin and a positive gain margin, it is regarded as stable. Better stability and robustness are indicated by higher phase and gain margins.
Stability Analysis
A crucial stage in the design of a control system is stability analysis. It entails examining the system's transfer function or state-space model's poles and zeros. The system's stability is directly influenced by where these poles and zeros are situated in the complex plane.
You can compute the poles and zeros of a control system using MATLAB's pole and zero functions. The root locus plot, produced by the rlocus function, displays how the system's poles alter in response to different PID gains. Engineers can comprehend the stability characteristics and make the necessary adjustments to ensure stability by analyzing the root locus.
Performance Metrics
These performance metrics can be computed and displayed using MATLAB's step response plots and other analysis tools. Engineers can use this knowledge to adjust the PID gains and enhance the performance of the controller for particular applications.
Common Challenges in MATLAB Assignments on PID Controllers
Although MATLAB is an effective tool for PID controller design, students frequently run into a number of problems when working on assignments on this subject.
Tuning Parameters
Iterative and complex processes can be involved in PID controller tuning. Students must comprehend how each gain affects the system's response and use the appropriate tuning techniques as a result. Additionally, the tuning strategy may change depending on the control goals and dynamics of the system.
Students should experiment with various tuning methods to overcome this difficulty and use MATLAB's autotuning functions to automate the procedure and find the best PID gains for the given system.
Modeling Complex Systems
Because real-world systems are frequently complex, non-linear or multivariable control strategies may be necessary. Students must be familiar with these tools in order to use the advanced functions provided by MATLAB's Control System Toolbox to manage such complexity.
Students who work with complex systems can model the system using transfer functions or MATLAB's state-space representation. The system can be divided into smaller subsystems so that students can create unique controllers for each one before combining them to control the entire system.
Handling Constraints
When designing the PID controller for some applications, physical restrictions on actuators or sensors must be taken into account. It can be difficult to incorporate these constraints into the control system.
Students can overcome this difficulty by using the optimization toolbox in MATLAB to make sure the PID controller operates within the defined constraints. They should also run MATLAB simulations to confirm the controller's effectiveness under constraint conditions.
Conclusion
PID controller design is a fundamental component of control engineering, and MATLAB offers a great platform for investigating and putting different control strategies into practice. PID controllers are crucial for successful control system design because they can help control systems achieve stability and performance.
PID controller design problems, like tuning, stability analysis, and constraint handling, can be effectively handled with the help of MATLAB's Control System Toolbox, Simulink, and optimization functions. Mastering PID controller design in MATLAB opens doors to a world of possibilities in the field of control systems, whether for academic assignments or real-world applications. The future of PID controller design looks even more promising with ongoing enhancements and updates to MATLAB's capabilities, allowing engineers and researchers to successfully tackle control problems that are getting more complex.